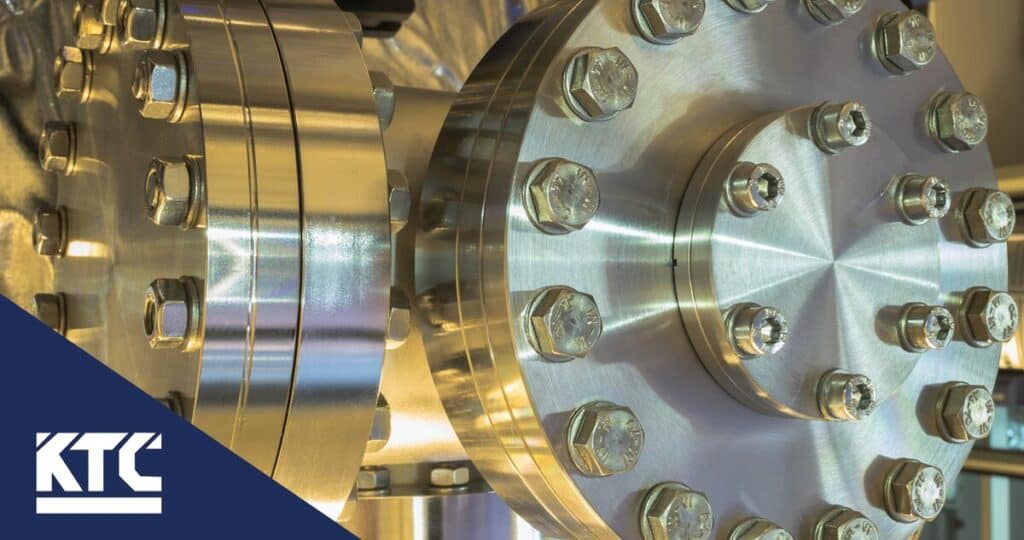
Vacuum chambers are used in several industries, semiconductor manufacturing being one of the most demanding. Precision and repeatability are critical in the production of integrated circuits, or microchips, and vacuum chambers play a critical role. Vacuum chambers serve to create a controlled environment where processes take place in a vacuum or low pressure-controlled conditions. In this blog post, we delve into the basics of vacuum chamber manufacturing, shedding light on the essential elements that make these chambers indispensable in semiconductor manufacturing.
The Role of Vacuum Chambers
Vacuum chambers are specialized enclosures designed to create and maintain a low-pressure environment by degassing and creating a vacuum – typically 10^-6 to 10^12 Torr. This pressure-controlled atmosphere is vital for semiconductor manufacturing, where even the slightest interference from particulates, outgassing, or leaks can compromise the intended result. Vacuum chambers facilitate processes such as thin-film deposition, material testing, and ion implantation.
Vacuum Chamber Materials Matter
One of the fundamental aspects of vacuum chamber manufacturing is the selection of materials. Given the stringent requirements of the semiconductor industry, these chambers must be constructed from materials that can withstand extreme conditions while maintaining a high level of purity. Stainless steel and aluminum are commonly used vacuum chamber materials, due to their resistance to corrosion and ability to maintain structural integrity under vacuum conditions. To achieve certain magnetic properties, Keller Technology has also constructed chambers from carbon steel which is subsequently nickel plated.
Customization for Varied Applications
Although vacuum chamber manufacturing is very often build-to-print, manufacturers can design and create vacuum chambers tailored to specific applications, accommodating the unique needs of customers that are semiconductor equipment manufacturers – whether it’s a custom shape, size, or the addition of other specialized features.
Precision Machining & Welding Expertise
A critical aspect of vacuum chamber manufacturing involves tight-tolerance machining and fabrication, with a particular emphasis on precision welding. Achieving the desired vacuum levels and maintaining a leak-free environment demands meticulous attention to detail. Expert welders utilize advanced techniques to ensure the chambers meet exact specifications, with precision welding playing a key role in creating seamless and robust structures that withstand the demanding conditions of Ultra-High Vacuum (UHV)/ semiconductor processes.
Seals and Joints
An integral part of vacuum chamber manufacturing is the design and implementation of seals and joints. These components are critical for maintaining the vacuum within the chamber. High-quality gaskets such as knife edge conflates and wire seals are employed to create airtight closures, preventing any unwanted air from entering the chamber during operations.
Surfacing Treatment Options
Another crucial consideration in vacuum chamber manufacturing is the treatment of chamber surfaces. Various surfacing treatment options are employed to enhance performance and durability. Common treatments include chemical passivation or electropolishing, which improve corrosion resistance and remove contaminants from the surface, ensuring the chambers maintain their integrity over extended periods of use.
Vacuum Chamber Bakeout Process
In the vacuum chamber manufacturing process, the bakeout procedure is essential. This involves heating the chamber to high temperatures to remove any residual gases and contaminants. The bakeout process ensures the chamber is thoroughly clean and ready for semiconductor manufacturing operations, contributing to the vacuum chambers’ reliability and effectiveness.
Quality Control Measures
Given the high stakes involved in semiconductor manufacturing, rigorous quality control measures are imperative in vacuum chamber production. Each chamber undergoes stringent testing to ensure it meets the specified vacuum levels, maintains structural integrity, and is free from defects. Quality assurance processes include helium leak testing, RGA, pressure testing, and dimensional inspections to guarantee the reliability of the chambers.
Advanced Vacuum Chamber Manufacturing from Keller Technology
As technology advances and the application for smaller, faster microchips continues to expand, vacuum chamber manufacturing will continue to play a crucial role in enabling the cutting-edge innovations that will drive the industry forward. Contact Keller Technology for precision fabrication, custom machining and contract manufacturing.