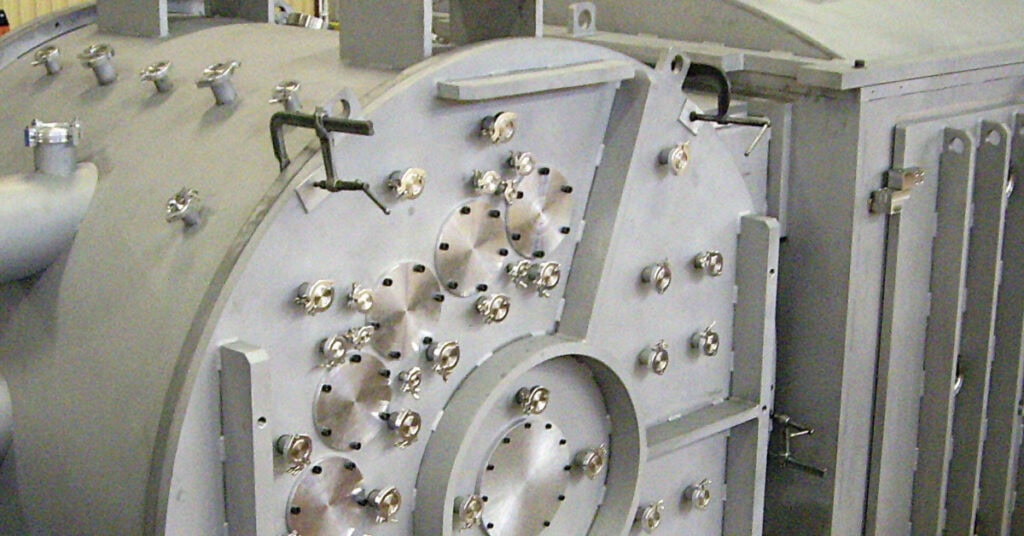
Thin Film Deposition System Case Study
Summary
This case study highlights our work in manufacturing a custom thin film deposition system for a manufacturer of advanced materials. The system was engineered to deposit materials with highly uniform thickness and chemical consistency onto a moving web substrate within a controlled vacuum environment. Our scope of work included fabricating custom vacuum chambers and robust external frame, integrating advanced mechatronics and developing a comprehensive control system. This project exemplifies our expertise in precision services such as manufacturing and fabrication services, system integration, and delivering high-quality solutions for advanced industrial applications.
Background
Keller Technology was selected as the contract manufacturer of a production run of large vacuum coating systems for the deposition of a film onto a web. The product was comprised of a large, custom fabricated aluminum vacuum chamber measuring approximately 9’ x 10’ x 12’ containing electro-mechanical assemblies including web unwind and rewind, web guidance and customer supplied sputtering equipment.
Thin film deposition is a cornerstone process in a variety of industries. From semiconductors and electronics to solar and household plumbing fixtures, each application is unique and requires applying ultra-thin layers of material onto a substrate to achieve specific functional or aesthetic properties. In this case, the client required a system designed for continuous web coating, where a flexible substrate moves continuously from an outfeed roll to a wind-up roll. The system operates in a vacuum environment to ensure process consistency and eliminate contaminants. Achieving uniform film thickness and chemical consistency was critical for the client’s application.
Client Description
The client is a globally recognized leader in manufacturing equipment for advanced material deposition. Their products also include high-performance coated substrates used for applications such as flexible electronics, renewable energy, and specialty coatings. As a company known for innovation, they prioritize precision and consistency in their manufacturing processes to meet stringent quality and performance standards. For this project, the client sought a cutting-edge thin film deposition system that could enhance their production capabilities, enabling them to maintain a competitive edge in a rapidly evolving market.
Project Goals and Objectives
The primary goal of this project was to manufacture a thin film deposition system capable of delivering consistent, high-quality coatings across a moving web substrate. Specific objectives included:
- Custom Vacuum Chambers: Fabricating both cylindrical and box-type vacuum chambers capable of maintaining a high-vacuum environment while accommodating the internal deposition components.
- Advanced Mechatronics: Developing custom mechatronic systems to control web movement and optimize deposition precision. These systems needed to function reliably within the vacuum environment.
- Structural Integrity: Constructing an external frame to support the chambers and ensure system stability during operation.
- Control System Integration: Creating an advanced control system to regulate deposition conditions, synchronize component operations, and provide real-time monitoring for process consistency.
As Keller is not an expert in the physics of vacuum deposition, meeting these objectives required a collaborative approach between our engineering team and the client – ensuring every design and fabrication decision aligned with the client’s operational needs.
Challenges Faced
Technical Challenges
- Ensuring the uniform deposition of thin films across a moving web presented significant engineering challenges. Achieving consistency required precise calibration of deposition parameters, including substrate speed, material flow rate, and environmental conditions within the vacuum chamber.
- Developing vacuum chambers that maintained vacuum integrity while integrating complex mechatronics and deposition components was technically demanding. The chambers needed to accommodate both static and dynamic operations while ensuring minimal contamination risks.
- Developing control systems that synchronized the movement of the web, the deposition process, and the mechatronic systems required advanced software and hardware integration.
Operational Challenges
- The complexity of the thin film deposition system demanded rigorous testing and validation at every stage.
- Coordinating efforts across multidisciplinary teams, including mechanical engineering, electrical engineering, and software development, required seamless communication and project management.
- Fabricating and assembling high-precision components, such as the vacuum chambers and mechatronics, demanded strict adherence to quality standards and thorough inspection protocols to ensure reliability and performance.
Results and Outcomes
The project was completed successfully, delivering a thin film deposition system that met or exceeded the performance expectations. Key outcomes included:
- Uniform Thin Film Deposition: The system achieved the client’s stringent requirements for material thickness and chemical uniformity, ensuring consistent product quality across all coated substrates.
- Reliable Operation: The integration of custom mechatronics and a robust control system ensured smooth, continuous operation with minimal downtime, enhancing production efficiency.
- Manufacturing Excellence: The vacuum chambers, external frame, and internal mechatronics were fabricated and assembled with precision, ensuring durability and optimal performance under demanding operating conditions.
- Process Optimization: The advanced control system provided real-time monitoring and adjustments, enabling the client to fine-tune their deposition processes for maximum efficiency and product quality.
Client Satisfaction
The FAT verified the system’s performance. Subsequent commissioning and operation have demonstrated fabricated component reliability. With respect to the overall experience, the client specifically commended the collaborative approach taken throughout the project, which ensured that their operational needs were fully understood and addressed. The system has since become a cornerstone of their production capabilities, allowing them to maintain their position as an industry leader in advanced materials manufacturing.
Conclusion
This project underscores our capabilities in delivering complex, precision-engineered systems for advanced industrial applications. By addressing technical and operational challenges through innovative engineering, meticulous quality control, and close collaboration with the client, we delivered a system that not only met but exceeded expectations. The successful completion of this thin film deposition system reaffirms our commitment to excellence in manufacturing and system integration.
Lessons Learned
Key takeaways from this project include:
- Client Collaboration: Working closely with the client and maintaining open lines of communication throughout the project was critical to meeting their specific needs and ensuring project success.
- Multidisciplinary Expertise: Combining mechanical engineering, mechatronics, and advanced control system development was essential to achieving the project’s goals.
- Rigorous Testing: Conducting thorough testing and quality assurance at every stage ensured the system’s performance and reliability.
- Flexibility and Problem Solving: Addressing challenges promptly and adapting to new requirements during the project lifecycle contributed to its success.
These insights will inform our approach to future projects, enabling us to continue delivering exceptional results for our clients. Contact us today to get started with your next project.