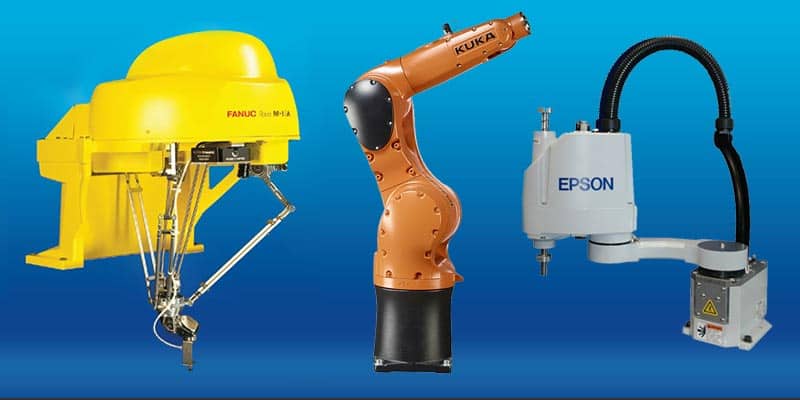
- The use of robotics in modern manufacturing facilities continues to grow.
- SCARA, Articulated, Cartesian or Gantry and Delta robots all have pros and cons when used in a factory setting.
- KTC has decades of experience integrating all four types of industrial robots to solve manufacturing problems.
To compete in the global economy, many companies are expanding the use of different types of industrial robots in their modern manufacturing facilities. If you aren’t familiar with the four main types of robots, now is the time to start doing some robotics research and learning the strengths and weaknesses of each kind and their common uses.
There are certainly other, less-common types of industrial robots, and sometimes one or more of the main kinds are combined to form a hybrid. However, these four different types are the configurations that you’re most likely to find working tirelessly in a modern factory.
- SCARA (Selective Compliance Assembly Robot Arm) – The robotics parts most often found with this type are four total axes of motion, three rotary axes and one linear Z-axis. The axis #1 base and #2 “elbow” joint are rotary, so the work zone is a circular shape. Axis #3, the Z-axis, adds thickness or height. These robots are generally used for high-speed assembly or material handling applications. Standard sizes range from very small to medium. There are variants where axis #1 is a linear rail instead of a rotary joint to extend the work zone into a more rectangular shape. For “clean room” applications, a rubber bellow is often added to the Z axis.
- Articulated – This kind of industrial robot is most often found in factories as a six rotary joint “arm” configuration. Four-axis, “palletizing” variants are also very common in today’s modern factories. Since all of the joints are rotary, the work zone is again circular. Arguably the most versatile style of robot, they are often mounted to walls and ceilings to reduce the overall footprint of the system. Sizes range from small to very large. A big advantage of this configuration is the relative ease of sealing rotary joints versus linear slides. For this reason, these kinds of robots are often used in very dirty or very clean environments. This robot style can also be mounted to a seventh axis “linear rail” to extend its working zone.
- Cartesian or Gantry – This robot type is generally made up of three linear sliding axes. The robot’s work zone area is the shape of a square or rectangle (X, Y) and the third, Z-axis, adds height. This kind of robot is a good choice for moving parts between trays and a machine’s processing nest. These robots can also be made to cover very large areas or reach deep into part dunnage. The disadvantage of this robot type is that they are generally slower than the other robot types. It is also difficult to keep dirt out of the sliding elements if the environment is dusty.
- Delta – Also called a “spider” robot, this type uses three servo motors and jointed parallelograms to position a tooling plate within a spherical work zone. These robots are very high speed and best suited for extremely light-duty tasks within small work zones. Because of these attributes, they are most commonly used for high-speed sorting and packaging in the food, pharmaceutical and electronics industries.
Note: Each of these different robot types has a “common” number of linear or rotary axis or joints. Each servo motor is numbered, generally from the largest to the smallest, starting with joint or axis #1 at the base.
Keller Technology Corporation (KTC) has decades of experience integrating all of these four main types of industrial robots.