- There are a wide variety of Additive Manufacturing (AM) systems creating parts out of an assortment of materials.
- Engineers are learning to design parts for new AM systems.
- AM is changing the way products are being designed and parts are being produced.
Additive Manufacturing, or AM, is the process of creating a three-dimensional object directly from digital data. A part model, created using a computer and CAD software, is physically recreated, layer by layer, on the printer’s build platen utilizing feedstock materials in liquid, powder, filament, or sheet forms.
There are a wide variety of AM systems creating parts out of many materials, including polymer, plaster, metallic, glass, concrete, paper, ceramic, and biologics. From nanometer scale to the size of a house, AM is producing complex geometry and details that cannot be created by any other manufacturing process.
Engineers are learning to design parts specifically for these new AM processes, and it is changing manufacturing as we know it. Here are the seven categories of systems, as defined by the Additive Manufacturing Research Group, and a brief synopsis of each type:
- Material Extrusion – In its most common form, a polymer filament is drawn through a heated nozzle, melted, and then deposited layer by layer forming the three-dimensional part geometry. It is common for the nozzle to move sideways in the “X” and “Y” axis, and the build platen to move up/down in the “Z” axis. Extremely large versions of this printer type pump a stiff concrete mortar material to a programmable, three-axis, nozzle and print entire homes on the designated build site.
- Sheet Lamination – Printers in this category use a flat feedstock material in the form of rolls, ribbons, sheets, or strips. A system utilizing metallic materials bonds layers together via ultrasonic energy. Another system uses standard copy machine paper, ink, and glue to create full-color, 3D objects in stunning detail.
- Directed Energy Deposition (DED) – This process can be used with polymers and ceramics as well, but it is often used with a metallic feedstock that is introduced to the machine in powder or wire form. DED systems generally consist of a spray nozzle mounted on a programmable, multi-axis, robotic arm that directs a stream of melted material onto the targeted build surface where it solidifies. The added energy required to liquefy the metal can be introduced into the system in the form of high electrical current, laser or electron beam. One unique system uses gas jets to accelerate metal particles to supersonic speed. Upon the particle’s collision with the stationary target, the sheer kinetic energy causes the metal to deform and stick to the substrate.
Stereolithography (SLA) – This category of machine uses a vat of liquid photopolymer resin as its material feedstock. A computer-controlled, ultraviolet light projection system exposes the photopolymer to an “image” of each individual layer of the object being produced. As each layer is cured, the motorized build platen repositions the “Z” axis of the part within the vat of uncured resin. As the process uses liquid to form objects, there is no structural support from the material during the build so support structures will often need to be added. The process of photopolymerization is relatively fast compared to the other additive manufacturing processes; therefore, this type of printer is already being used by large global companies to produce consumer products such as the soles of running shoes and protective cases for cell phones.- Material Jetting – This process creates objects in a similar method to a two dimensional ink jet printer. Liquid feedstock material is jetted via a nozzle(s) into the build envelope using either a thermal or piezoelectric dispensing method. The material solidifies by cooling, evaporation or exposure to UV light. Capable of nanoscale precision, machines of this type vary in complexity and in their method of guiding the droplets of material. This process allows for multiple materials within the same part and also the printing of biologic materials in controlled environments.
Powder Bed Fusion – This process includes Direct Metal Laser Sintering (DMLS), Electron Beam Melting (EBM), Selective Heat Sintering (SHS), Selective Laser Melting (SLM) and Selective Laser Sintering (SLS). All of these methods use either a laser or electron beam to fuse particles together and require the spreading of a powder feedstock material over previous layers. A roller or a blade sweeps a uniform layer of material, from an adjacent hopper of powder, over the part. The programmable beam of energy sinters the powder, layer by layer. On the other hand, SHS differs from the other processes because it uses a heated thermal print head to fuse the granules of powder together.- Binder Jetting– This process is similar to the Powder Bed Fusion process in many respects, however, it uses two materials; a powder-based feedstock material and a liquid binder. The binder is an adhesive and provides a temporary bond between the powder particles and also the powder layers. A programmable nozzle moves horizontally along the “X” and “Y” axes of the build area and deposits a precise amount of the binder in the desired locations. After printing of the part geometry is completed, the part is sintered in a furnace which burns away the binder and fuses the powder particles together. The post-process fusing does shrink the part; however, this size reduction is consistent and predictable and is compensated for during planning.
AM is changing the way consumer products are designed and component parts are being produced. With newer and more powerful software becoming available and as evolving 3D printing processes being invented, it’s only a matter of time before every consumer benefits from this new manufacturing technology. Keller Technology Corporation is excited to see what the future has in store for the factories of the future.
Take your applications to the next level
With over 100 years of experience, Keller has adapted to the ever-changing processes of manufacturing and engineering. Let us take your contract manufacturing project to the future.
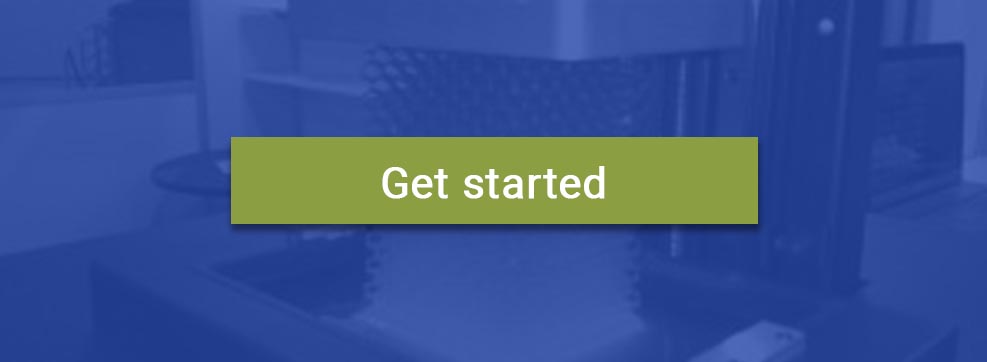