Vacuum Chamber Testing: Helium Leak Testing & Residual Gas Analysis (RGA)
Vacuum chambers play a crucial role in numerous high-tech industries, including semiconductor manufacturing, aerospace, and energy research. To ensure optimal performance, these chambers must maintain a completely sealed environment, as even minor leaks or contamination can significantly impact their functionality. This is where helium leak testing and residual gas analysis (RGA) come into play. Both techniques are vital for verifying the integrity of vacuum chambers, helping to ensure they meet stringent performance requirements. In this blog, we’ll explore these essential testing methods and explain how Keller Technology Corporation utilizes them to deliver reliable, high-performance vacuum chambers.
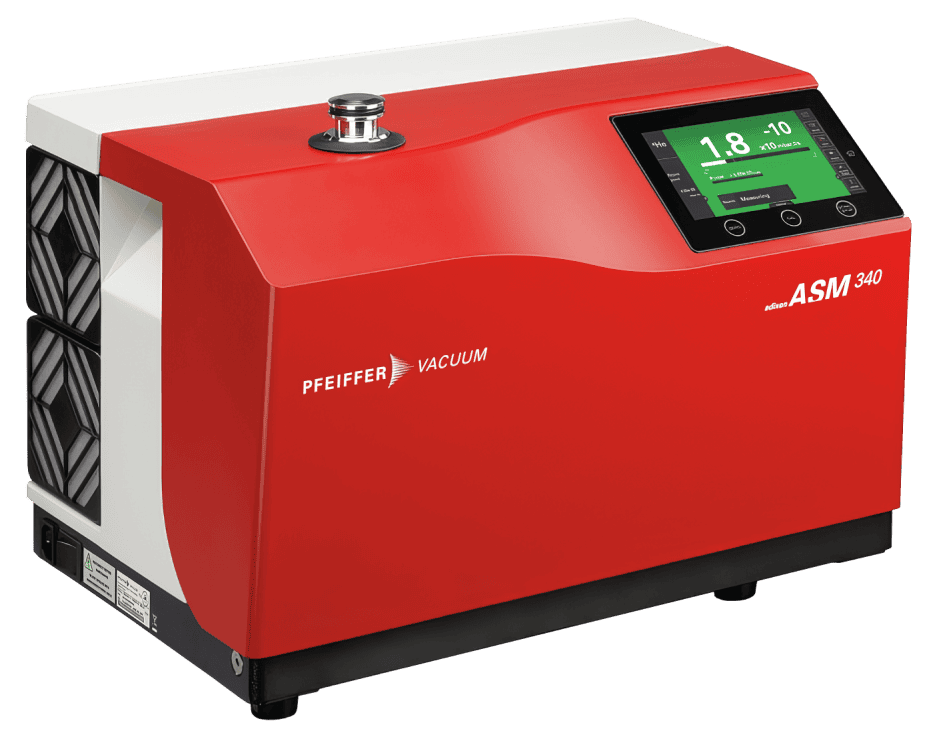
Helium Leak Testing
Helium leak testing is known for its high sensitivity and is capable of detecting vacuum chamber leaks as small as 10^(-9) mbar·L/sec. Helium, a light and inert gas, is ideal for this purpose due to its small atomic size and non-reactive properties, enabling it to penetrate tiny leaks that gases like air or nitrogen might miss. The main objective of helium leak testing is to identify any potential entry or exit points for gases, ensuring that the vacuum chamber is properly sealed. This is particularly crucial in applications such as semiconductor equipment, where the presence of unwanted gases can significantly affect product quality and operational efficiency.
How Helium Leak Testing Works
To conduct a helium leak test on a vacuum chamber, helium is introduced to the interior or the exterior of the vacuum chamber. Then a helium mass spectrometer is used to detect the presence of the gas. There are two primary methods of conducting helium leak tests:
Vacuum Method:
In this method, the vacuum chamber is evacuated, and helium is sprayed around its exterior. If any helium enters the chamber through leaks, the mass spectrometer detects it and provides precise information about the leak’s location and size. This method is extremely sensitive and can detect even the smallest leaks.
Sniffing Method:
The sniffing method is typically used for larger leaks or when the vacuum method is not practical. Helium is introduced inside the chamber, and a “sniffer” probe is used to detect escaping helium on the chamber’s exterior.
Residual Gass Analysis (RGA)
What Is Residual Gas Analysis (RGA)?
While helium leak testing ensures that no external gases are entering the vacuum chamber, residual gas analysis (RGA) focuses on the detection and identification of gases already present inside the chamber. This is essential because even minute quantities of contaminants can degrade the performance of a vacuum chamber and jeopardize the processes that occur within.
A residual gas analysis (RGA) typically consists of a mass spectrometer that analyzes the types and quantities of gases present inside the vacuum chamber. By measuring the molecular composition of these gases, the RGA can detect contamination or leaks within the vacuum chamber that might otherwise go unnoticed.
How a Residual Gas Analysis Works
Residual Gas Analysis operates by ionizing the gas molecules inside the vacuum chamber and then separating them based on their mass-to-charge ratio. The system can detect a wide range of gases, including water vapor, oxygen, nitrogen, carbon dioxide, and more harmful contaminants like hydrocarbons or solvents. This real-time analysis of gas composition provides critical insights into the chamber’s vacuum integrity, enabling technicians to clean, adjust, or make repairs if unwanted gases are detected. RGA is particularly useful when combined with helium leak testing, as it can help identify contamination issues that might be unrelated to leaks, such as outgassing from materials inside the chamber.
Applications of Helium Leak Testing & Residual Gas Analysis
Helium leak testing and Residual Gas Analysis are indispensable in industries that require high levels of vacuum integrity, including:
- Semiconductor Manufacturing: Where vacuum chambers are essential for processes like deposition and etching.
- Aerospace: For testing components exposed to space-like environments.
- Energy Research: Where contamination or leaks could compromise the safety and functionality of the equipment.
In each of these industries, the ability to maintain a stable, uncontaminated vacuum chamber environment is crucial for ensuring product quality and meeting stringent industry standards.
How Keller Technology Ensures Vacuum Integrity
At Keller Technology Corporation, we prioritize vacuum chamber integrity by utilizing advanced helium leak testing and residual gas analysis systems. Equipped with the latest technology, we ensure every vacuum chamber meets the highest standards for leak-tightness and gas purity. These testing methods have been successfully applied across complex projects, from semiconductor equipment to high-pressure vessels, guaranteeing reliable performance in even the most demanding environments.
Contact Keller Technology
Learn more about our helium leak testing and residual gas analysis services or get help with your next vacuum chamber project. Contact us today to discuss your specific requirements.